Setting Up Vendor Managed Inventory
To set up VMI replenishment at the business unit level, use the BU Replenishment (IN_VMI_REPLN_BU) component. To set up VMI items at the business unit level, use the BU Item Replenishment (IN_VMI_RPLN_BUITEM) component.
To set up ship to information, use the Ship-To/Item Replenish (IN_VMI_RPLN_SHIPTO) component.
When setting up your system to manage stock at a customer location, you must:
Set up security for the VMI manager.
Define items by SetID.
Create a VMI business unit.
Set up Ship To VMI options for the customer.
Set up Sold To options for the customer.
Define items for a VMI business unit.
Create storage locations for the VMI business unit.
Setup VMI Replenishment parameters.
Setting Up VMI Replenishment Parameters
VMI replenishment parameters can be set up at these levels:
The customer ship-to level.
The VMI business unit level.
The VMI business unit and item combination level.
The VMI business unit, item, and customer ship to level.
Replenishment parameters default from different places. They may be defined at the customer ship-to and item combination level. If they are not, this table illustrates the manner in which they will default:
Replenishment Attribute |
Primary Default Source |
Second Default Source |
Third Default Source |
Fourth Default Source |
---|---|---|---|---|
Replenish Class |
VMI Ship-To Item Attributes |
VMI BU Item Replenishment |
||
Reorder Quantity Option |
VMI Ship-To Item Attributes |
Ship-To Customer |
VMI BU Item Replenishment |
VMI BU Replenishment |
Stock-in Rate |
VMI Ship-To Item Attributes |
Ship-To Customer |
VMI BU Item Replenishment |
VMI BU Replenishment |
Replenish Calculation Period |
VMI Ship-To Item Attributes |
Ship-To Customer |
VMI BU Item Replenishment |
VMI BU Replenishment |
Reorder Point Range Checking |
VMI Ship-To Item Attributes |
Ship-To Customer |
VMI BU Replenishment |
|
Reorder Point Percent |
VMI Ship-To Item Attributes |
Ship-To Customer |
VMI BU Replenishment |
|
Reorder Point |
VMI Ship-To Item Attributes |
VMI BU Item Replenishment |
||
Maximum Quantity |
VMI Ship-To Item Attributes |
VMI BU Item Replenishment |
||
Replenish Lead Time |
VMI Ship-To Item Attributes |
VMI BU Item Replenishment |
||
Reorder Quantity |
VMI Ship-To Item Attributes |
VMI BU Item Replenishment |
||
Economic Order Quantity |
VMI Ship-To Item Attributes |
VMI BU Item Replenishment |
||
Source Business Unit |
VMI Ship-To Item Attributes |
Ship-To Customer |
||
Product ID |
VMI Ship-To Item Attributes |
VMI BU Item Replenishment |
First record found in the PROD_ITEM table for the inventory business unit SetID |
|
Unit or Measure |
VMI Ship-To Item Attributes |
VMI BU Item Replenishment |
Default UOM for the product in the PROD_UOM table |
Item Standard UOM |
Page Name |
Definition Name |
Usage |
---|---|---|
USER_ROLES |
Assign the VMI Manager role to the user ID, which enables the user to access VMI components. PeopleTools : Security Administration |
|
ITEM_DEFIN |
Define items at the SetID level. |
|
BUS_UNIT_INV1 |
Define a VMI business unit. |
|
CUST_SHIPTO_OPT2 |
Define VMI options for the ship to customer. |
|
CUST_SOLDTO_OPT |
Define VMI options for the sold to customer. |
|
STORAGE_AREA_INV |
Used to create storage areas for a VMI business unit. |
|
STOR_LOCATIONS_INV |
Used to create storage locations for a VMI business unit, and associate the customer to the location. |
|
GEN_ATTRIB_INV |
Add a cost element and define VMI customers for the VMI business unit and item combination. |
|
IN_LOC_SHIP_TO_SP |
Used to define customer ship to locations for the business unit. |
|
IN_VMI_RPLN_BU |
Used to define replenishment parameters for a VMI business unit. |
|
IN_VMI_RPLN_BUITEM |
Used to define replenishment parameters for a VMI business unit and item combination. |
|
IN_VMI_RPLN_SHIPTO |
Used to define replenishment parameters for a VMI business unit, item, and customer ship to combination. |
Use the User Profiles - Roles page (USER_ROLES) to used to assign the VMI Manager role to the user ID, which enables the user to access VMI components.
Navigation:
. Select the Roles Tab.
Use the Define Item-General: Common page to define items for VMI usage.
Navigation:
In the Item Type group box, make sure that the Non-Owned Item and the Consigned Purchase check boxes are not selected.
Use the Business Unit Definition page (BUS_UNIT_INV1) to create a VMI business unit that represents your customer site.
Navigation:
Select the VMI Stock check box to indicate that this business unit is supplier managed.
Note: The VMI business unit must have the same general ledger business unit as the supplying inventory business unit.
Use the Ship To - VMI Options page (CUST_SHIPTO_OPT2) to define VMI options for the ship to customer.
Use the Customer Ship To Options page to indicate that the customer accepts partial scheduled and partial orders so that the VMI manager can examine back ordered quantities.
To indicate that a customer ID is a VMI managed location, use the Customer Information (CUSTOMER_GENERAL) component. Use the Customer Ship To (CUSTOMER_SHIPTO_CI) component interface to load data into the tables for this component.
Navigation:
VMI Options link.
. Select the Ship To Options tab, then select theThis example illustrates the fields and controls on the Customer Ship To - VMI Options page. You can find definitions for the fields and controls later on this page.
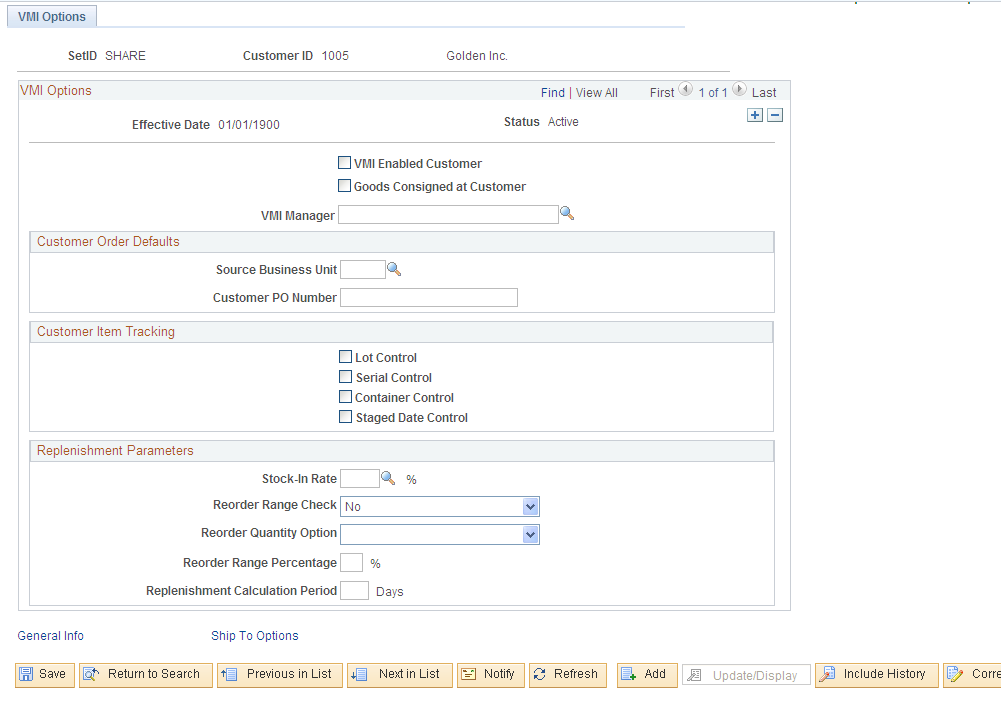
VMI Options
Field or Control |
Description |
---|---|
VMI Enabled Customer |
Select to indicate that this customer ship to ID stocks consigned items and is used for VMI. |
VMI Manager |
Select the employee who is responsible for approving and overseeing orders generated for the VMI customer. This employee must have a role of VMI Manager. |
Goods Consigned at Customer |
Select to indicate that items shipped to this customer are not owned by the customer and are not paid for until they are consumed. This customer is not billed for items when the items are shipped. If selected, the four customer item tracking options; lot control, serial control, container control, and staged date control are automatically selected when you save the page. If not selected, the four customer item tracking options are not affected. This option also determines the Non-Owned option on the Material Storage Locations page. |
Customer Order Defaults
Field or Control |
Description |
---|---|
Source Business Unit |
Select the inventory business unit that is used when the VMI Replenishment process generates sales orders. This inventory business unit indicates the typical ship from location. |
Customer PO Number |
Enter the customer purchase order ID that is included on the sales order acknowledgement. |
Customer Item Tracking
Select to indicate that lot, serial, container, and staged date information is maintained at the customer site. If selected, all transactions received from the customer will contain the item detail. If not selected, transactions received from the customer will not contain the item detail, and the items are depleted by using FIFO logic.
The options can not be updated if there is inventory on-hand or in-transit to the ship-to customer.
If any of the four customer item tracking options are selected, they are not grayed-out when you save. Instead, they are grayed-out the next time you access the page.
Replenishment Parameters
Indicate specific replenishment parameters that are used to calculate replenishment requests for VMI.
Use the Sold To Options page (CUST_SOLDTO_OPT) to define VMI options for the sold to customer.
To set up customer sold to VMI options, use the Customer Information (CUSTOMER_GENERAL) component. Use the Customer Sold To (CUSTOMER_SOLDTO_CI) component interface to load data into the tables for this component.
Navigation:
. Select the Sold To Options tab.
This example illustrates the fields and controls on the Sold To Options page. You can find definitions for the fields and controls later on this page.
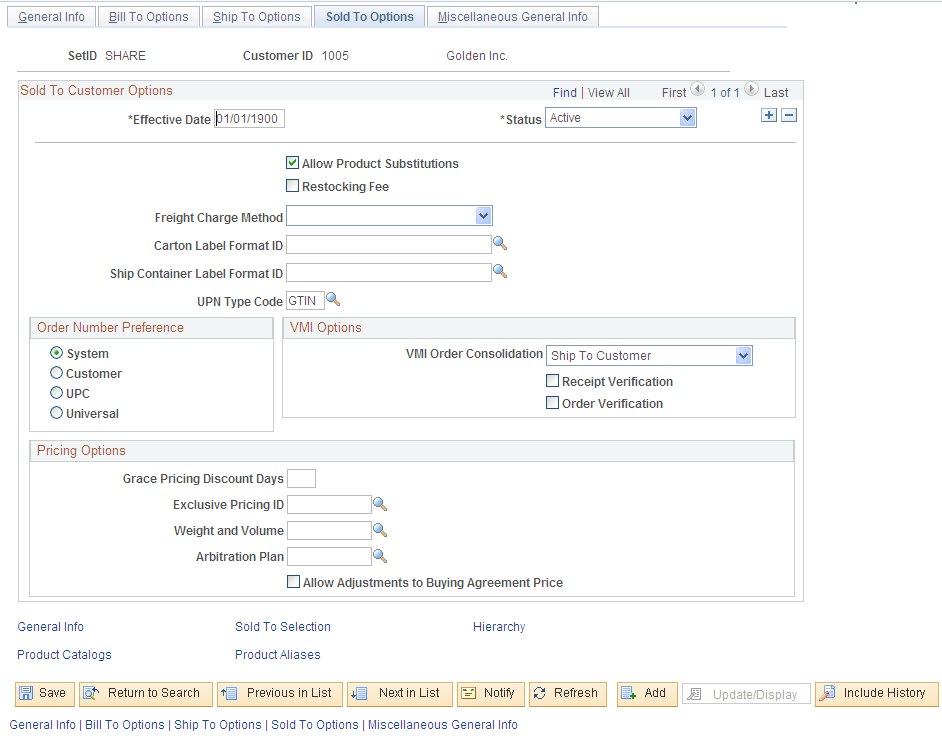
Field or Control |
Description |
---|---|
VMI Order Consolidation |
Select the option that determines how sales order requests, that are generated during the VMI Replenishment process, is grouped. None: Select to instruct the VMI Replenishment process to generate a separate sales order for every replenishment request. Ship To Customer: Select to instruct the VMI Replenishment process to combine all replenishment requests for the same ship to customer on the same sales order or material stock request. Sold To Customer: Select to instruct the VMI Replenishment process to combine replenishment requests for the same sold to customer on the same sales order. This applies only to sales orders for non-consigned customers. |
Receipt Verification |
Select to indicate that the customer wishes to verify the receipt of items. If selected, the customer acknowledges the receipt of goods at their site. Shipments will appear as being in-transit until the receipt verification is received. If not selected, the customer does not acknowledge receipt, and the auto-putaway process is used to update on hand quantities for the VMI business unit. |
Order Verification |
Select to indicate that all sales orders created for this customer go on VMI hold. This provides the VMI manager to review the order before releasing it from hold. |
Use the Define Business Unit Item-General: Common page (GEN_ATTRIB_INV) to define items for a VMI business unit.
Navigation:
Add a cost element. The Non-Owned Item and Consigned Purchase options are not enabled.
Use the Material Storage Locations - VMI Ship To page (IN_LOC_SHIP_TO_SP) to used to define customer ship to locations for the business unit.
Navigation:
. Select the VMI Ship To link.
This example illustrates the fields and controls on the Material Storage Locations - VMI Ship To page. You can find definitions for the fields and controls later on this page.
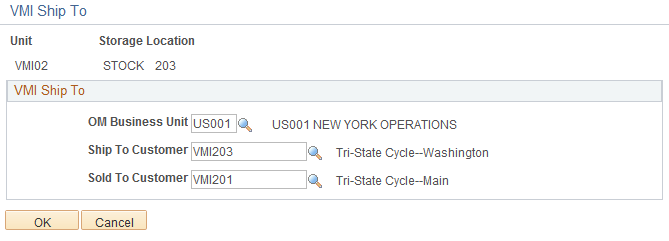
Use the Material Storage Locations page to create storage location for the VMI business unit. Then use the Material Storage Locations - VMI Ship To page, to enter the VMI Order Management business unit, the VMI Ship To Customer identification code, the VMI Sold to Customer identification code, the Reorder Quantity Option, and the Desired Stock-In Probability.
Multiple customer ship to locations can be managed in one VMI business unit because the customer is associated to a material storage location. Therefore you can set up multiple MSLs within a VMI business unit; each MSL representing a customer site. If the customer site stores consigned and non-consigned items, you will need to create two storage locations and two customer ship-to values.
On the Material Storage Locations page, the Nettable, Non-Owned and WIP fields are not enabled. The Non-Owned field appears by default from the Goods Consigned at Customer option on the Customer: Ship To-VMI Options page.
Use the Customer Ship To - VMI Options page to set up VMI replenishment parameters for a customer ship-to.
Navigation:
. Select the Ship To Options tab, then select the VMI Options link
Use the BU Replenishment page (IN_VMI_RPLN_BU) to used to define replenishment parameters for a VMI business unit.
Navigation:
This example illustrates the fields and controls on the BU Replenishment page. You can find definitions for the fields and controls later on this page.
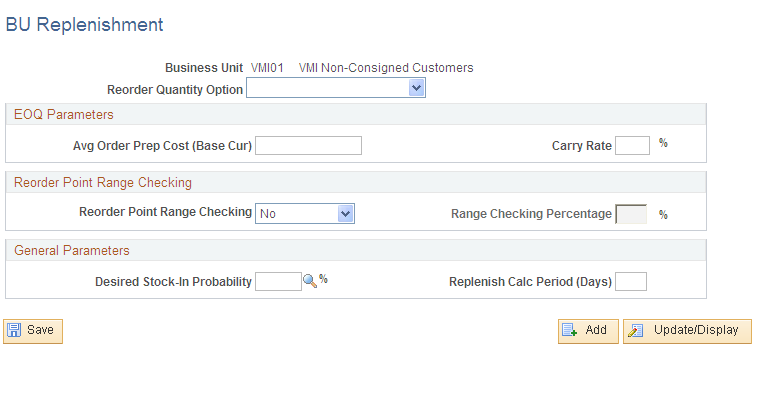
Field or Control |
Description |
---|---|
Reorder Quantity Option |
Select how the VMI items are replenished for the VMI business unit. Options are EOQ, Min/Max, and Static Reorder Qty. |
Use the BU Item Replenishment page (IN_VMI_RPLN_BUITEM) to used to define replenishment parameters for a VMI business unit and item combination.
Navigation:
This example illustrates the fields and controls on the BU Item Replenishment page. You can find definitions for the fields and controls later on this page.
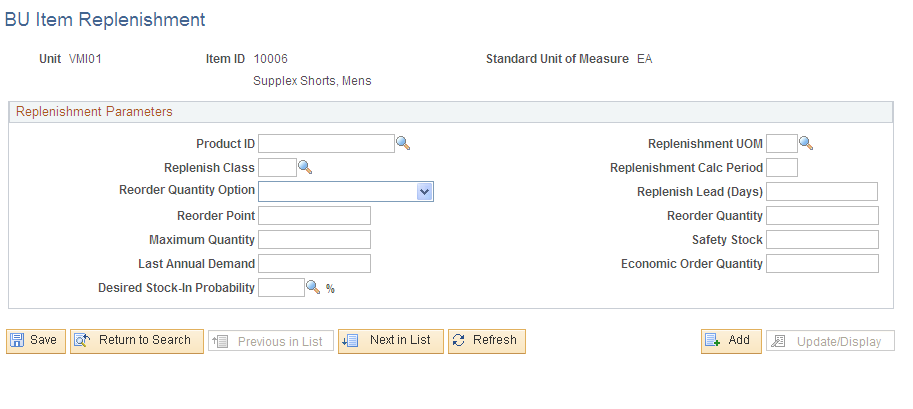
All values on this page override setup on the BU Replenishment page.
Field or Control |
Description |
---|---|
Replenish Lead (Days) |
This value represents the average number of days from the placement of a sales order or an MSR, to the receipt of the stock. |
Use the Ship-To/Item Replenishment page (IN_VMI_RPLN_SHIPTO) to used to define replenishment parameters for a VMI business unit, item, and customer ship to combination.
Navigation:
This example illustrates the fields and controls on the Ship-To/Item Replenishment page. You can find definitions for the fields and controls later on this page.

Field or Control |
Description |
---|---|
Replenish Lead (Days) |
This value represents the average number of days from the placement of a sales order or an MSR, to the receipt of the stock. This default value comes from the BU Item Replenishment page. |
The VMI Order Management business unit determines the SetID that is used when selecting the Ship To Customer.
The Source Business Unit appears by default from the Customer Ship To setup page.
All values on this page, override setup on the BU Replenishment page and the BU Item Replenishment page.