Refining and Viewing Sourcing Information Details
This topic discusses how to refine and view sourcing information details.
Page Name |
Definition Name |
Usage |
---|---|---|
PL_SRC_TMPL_INF |
Refine the sourcing template, including sourcing priorities and defaults, for an item. |
|
Review Business Unit Transfer Options Page |
PL_TRANS_BU_OPT |
Review default transfer attributes for ship via methods defined between source and destination business units, including transfer lead times and preferred order quantities. Review Business Unit Transfer Options or the Review Item Transfer Options Page |
Review Item Transfer Options Page |
PL_TRANS_IT_OPT |
Review item-specific transfer attributes for ship via methods defined between source and destination business units, including transfer lead times and preferred order quantities. Review Business Unit Transfer Options or the Review Item Transfer Options Page |
PL_PRODUCTION_OPT |
Review the production option (combination of BOM and routing), and its associated details, for an item. |
|
PL_PURCHASE_OPT |
Review the purchase option definition and associated details, such as buyer, supplier SetID, supplier ID, and supplier location, for an item. |
Field or Control |
Description |
---|---|
Maximum Order Quantity |
Displays the maximum quantity when creating new planned supplies. |
Minimum Order Quantity |
Displays the minimum quantity when creating new planned supplies. |
Order Multiple |
Displays the incremental quantity when creating new planned supplies. |
Planning Instance |
Click to access the planning instance information that includes basic information, dates, orders, and forecasts. |
Use the Review Sourcing Templates page (PL_SRC_TMPL_INF) to refine the sourcing template, including sourcing priorities and defaults, for an item.
Navigation:
This example illustrates the fields and controls on the Sourcing Templates page. You can find definitions for the fields and controls later on this page.
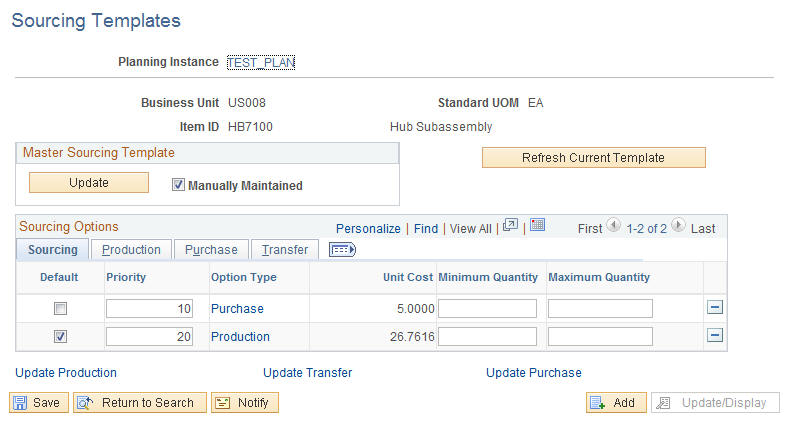
You can use this planning instance page to maintain sourcing templates within a planning instance and to copy changes made to planning instance sourcing templates directly back to the business unit (master) sourcing template. You can reset the Manually Maintained check box at the business unit sourcing template.
You can also replace the sourcing options for this planning instance with the business unit sourcing template options. Click the Refresh Current Template button to replace the existing sourcing options with the business unit sourcing template and if the business unit sourcing template does not exist, the system creates the default sourcing options. When the system prompts you, click Yes to refresh the current template with the current default sourcing options. Click No to keep the sourcing options as they appear on the page.
Note: When you click the Refresh Current Template button, the system copies the business unit (master) sourcing template to the planning instance sourcing template. If the business unit sourcing template doesn't exist, the system creates the default sourcing options.
Viewing or editing this page depends on whether the optimization engine is running. If the engine is running, the page will be display-only. If the planning engine is not running, you can edit the page and copy it to the master sourcing template.
Field or Control |
Description |
---|---|
Update |
Click to update the master sourcing template using the values from the planning instance template. A master sourcing template is a template that you set up for a business unit and inventory item; whereas, a planning instance sourcing template is one set up for a business unit and inventory item within a planning instance. When a master sourcing template exists, and you click the Update button, the system replaces the values on the planning instance. If the master template does not exist, the system creates it using values from this sourcing template. If the Manually Maintained check box is selected, the system updates the master sourcing template with the Manually Maintained check box selected. |
Manually Maintained |
Select to identify this sourcing template as a manually maintained template. If you select this check box, the Generate Sourcing Template batch job does not overwrite any options in the template. If you no longer need to maintain this sourcing template manually, deselect this check box. The next time that you run the Generate Sourcing Template batch job, the system overwrites the current sourcing template, including the options that you have defined. |
Sourcing
Select the Sourcing tab.
Field or Control |
Description |
---|---|
Default |
The system uses a default option to source demand when the planning engine cannot select other sourcing options because of capacity or material shortages. The Material solver uses the default option only when generating planned supply. Define at least one sourcing option as the default. |
Priority |
Displays the sourcing priority and sequence used by the Material and Capacity Feasible solver. |
Option Type |
Displays whether the demand is supplied by a production order, purchase order, or by a transfer order. |
Minimum Quantity |
When specified, identifies a minimum individual demand quantity that must be met before considering the related sourcing option. If the demand is greater than or equal to the minimum quantity specified, the system uses the sourcing option to generate the necessary supply. If the demand quantity is less than the minimum, the system does not consider the sourcing option a valid sourcing option. |
Maximum Quantity |
When specified, identifies a maximum individual demand quantity that is to be considered for the related sourcing option. If the demand quantity is less than or equal to the maximum quantity specified, the system uses the sourcing option to generate the necessary supply. If the demand quantity is greater than the maximum, the system does not consider the sourcing option a valid sourcing option. |
Production
Select the Production tab.
Field or Control |
Description |
---|---|
BOM (bill of material) |
Displays the BOM identifier for the production option in the template. Production options can be predefined or created based on defaults specified at the item attributes by unit level. |
Routing |
Displays the routing identifier for the production option in the template. This column is empty if you are not using routings. |
Associated Primary BOM (associated primary bill of material) |
For all of the secondary co-products, displays the primary co-product for which the BOM or routing exists. When an item is a co-product on multiple primary BOMs, then one of the primary co-products must be assigned as an associated primary BOM. The system uses the production option for the associated primary to generate supply for the secondary co-products. |
Purchase
Select the Purchase tab.
Field or Control |
Description |
---|---|
Supplier SetID |
Displays the SetID under which you define the supplier and purchasing information. |
Supplier ID |
Displays the supplier ID for the purchase option. |
Supplier Name |
Displays the supplier name for the supplier ID on the purchase option. |
Supplier Location |
Displays the supplier location used to create the purchase option. |
Buyer |
Displays the buyer ID associated with the purchase option supplier. Solvers assign this buyer when creating new planned purchases. If this buyer is blank, the solver assigns the primary buyer associated with the item. |
Transfer
Select the Transfer tab.
Field or Control |
Description |
---|---|
Source BU (source business unit) |
Displays the business unit that supplies the item. |
Ship Via |
Displays the method used for shipping the item. |
Use the Review Business Unit Transfer Options page (PL_TRANS_BU_OPT) to review default transfer attributes for ship via methods defined between source and destination business units, including transfer lead times and preferred order quantities.
Navigation:
Note: Unit-level transfer options are valid only for items defined with Distribution as the planned by value.
Field or Control |
Description |
---|---|
Ship Via Code |
Displays the method shipping the item. |
Intransit Days |
Displays the number of days required to transport completed units from one operation to the next. |
Intransit Hours |
Displays the number of hours required to transport completed units from one operation to the next. |
Transfer Yield |
Displays the usable output from the transfer. Expressed as a percentage, the transfer yield is used in PeopleSoft Supply Planning to inflate the planned quantity on transfers to account for any loss that occurs during transport. |
Use the Review Production Options page (PL_PRODUCTION_OPT) to review the production option (combination of BOM and routing), and its associated details, for an item.
Navigation:
Field or Control |
Description |
---|---|
Production Type |
Production options in PeopleSoft Supply Planning are always defined as Production. Rework and teardown production orders are visible to PeopleSoft Supply Planning but you cannot create new production of these types. |
BOM Code |
Displays the BOM identifier for the production option in the template. Production options can be predefined or created based on defaults specified at the item attributes by unit level. |
BOM Quantity |
Displays the BOM quantity used for scaling component quantity per assembly (QPA) for single output BOMs or the expected batch quantity expected for multiple output BOMs. |
Routing Code |
Displays the routing identifier for the production option in the template. If the corresponding item uses lead time instead of production routings, the system does not populate this field with a value. |
Fixed Lead Time |
Displays the fixed lead time of an item when generating planned orders without routings. |
Variable Lead Time |
Displays the variable lead time of an item when you generate planned orders without routings. |
Use Lead Time |
If selected, the associated item uses the fixed or variable lead times (instead of production routings) to schedule start and due dates for production. |
Expected Yield % (expected yield percentage) |
Displays the expected cumulative yield for the production order. PeopleSoft Supply Planning uses yield to inflate the starting quantity of production to account for loss that occurs during the manufacturing process. |
Effectivity Dates |
Displays the effectivity dates of the production option if the item is production option-controlled. |
Use the Review Purchase Options page (PL_PURCHASE_OPT) to review the purchase option definition and associated details, such as buyer, supplier SetID, supplier ID, and supplier location, for an item.
Navigation:
Field or Control |
Description |
---|---|
Lead Time Days |
Displays the purchasing lead time specified for the supplier or item and supplier relationship. This value represents the amount of time it takes to get inventory from the supplier. The value depends on the values selected in the Purchase Sourcing box on the Item Attributes: Planning tab. The lead-time value follows the hierarchy by checking for which purchase sourcing options are used. |
Purchase Yield |
Defines the usable output from the purchase. The value is expressed as a percentage. Purchase yield is used in planning to inflate the planned quantity on purchases to account for any loss that may occur during the purchase process. |