Running the Material Readiness Report
Before releasing production IDs and production schedules to the shop floor, you will want to determine which production orders have all of the material available and which production orders have material shortages. Production orders with all material available can be released to the shop floor. Production orders with shortages need to be investigated to determine when production can be released to the shop floor. Run the Material Readiness report to determine if the production ID or production schedule is ready to release and to view the quantities and readiness status of the components.
The Material Readiness report includes two to three sections:
Report Criteria section: This section details the options you have selected on the run control pages for the Material Readiness report.
Production Detail section: This section displays production readiness by production ID or production schedule. You produce this section by selecting the Production Report check box on the Material Readiness Report run control page.
Component Summary section: This section displays time-phased demand and supply quantities by component item ID and determines if there is enough available quantity to meet the demand. You produce this section by selecting the Summarized Component Report check box on the Material Readiness Report run control page.
This example illustrates the fields and controls on the Example of the Report Criteria section of the Material Readiness report. You can find definitions for the fields and controls later on this page.
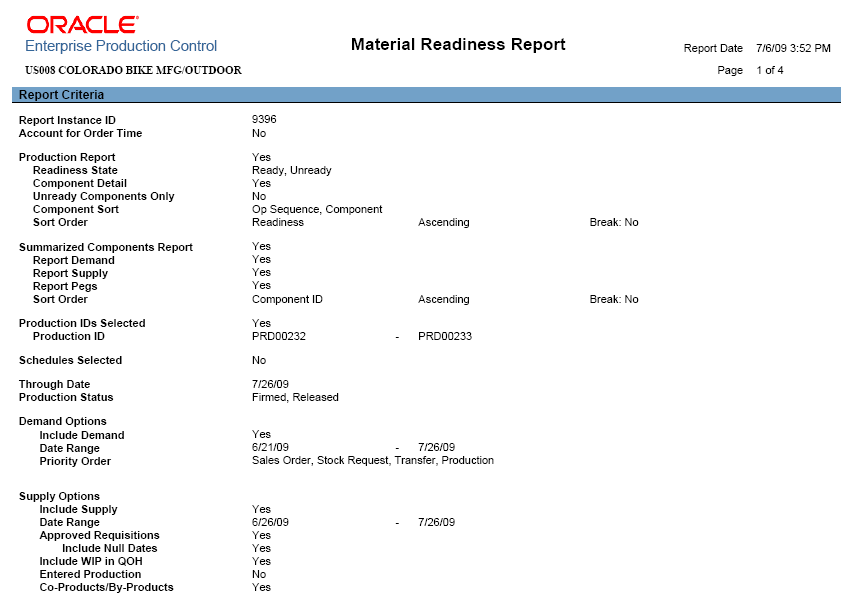
The report criteria section displays your selection criteria entered on the run control for the Material Readiness Report (Production Control, Process Production, Release Production, Material Readiness Report).
This example illustrates the fields and controls on the Example of the Production Detail section of the Material Readiness report. You can find definitions for the fields and controls later on this page.
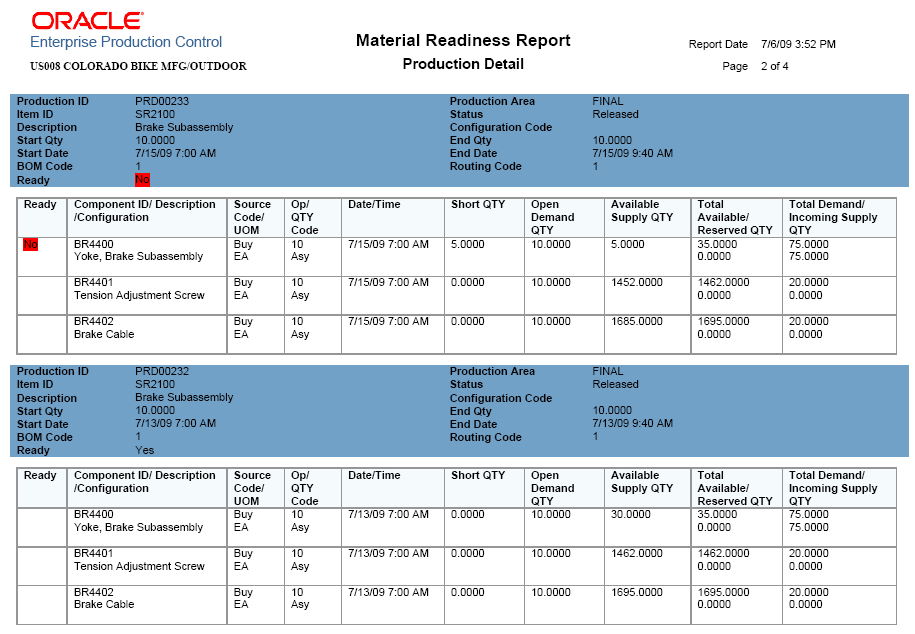
The production detail section of the Material Readiness report displays production readiness by production ID or production schedule. The quantities displayed on this report are calculated based on your selection criteria on the run control for the Material Readiness Report (Production Control, Process Production, Release Production, Material Readiness Report).
For each component in the production order, the following fields are displayed:
Field or Control |
Description |
---|---|
Ready |
Displays No when there is not enough quantity of a component to complete this production order on the date and time needed. For example, in the previous page shot, the item ID BR4400 in production ID PRD00233 is not ready because there is not enough supply on the date that the production ID needs the quantity. |
Component ID / Description / Configuration |
Displays the item ID and description of the component used in this production order. For configured items, the configuration code is displayed. |
Source Code/UOM |
Displays the source code of the component (such as Make or Buy) and the standard unit of measure of the component. All of the component's quantity fields on this report are expressed in this unit of measure. |
Op/QTY Code |
The Op Code field displays the operation sequence where this component is consumed within the production order. The QTY Code field displays the component requirements in amounts per Asy (assembly) or per Ord (order). |
Date/Time |
Displays the date and time that this component is needed for production based on the start date of the operation sequence using the component. |
Short QTY |
Displays the shortage of the component that is not available for this production order on the date and time needed. The shortage quantity is calculated using the following columns in the same row: Open Demand QTY field less Available Supply QTY field. If the Available Supply QTY field is greater than the Open Demand QTY field then enough stock is available and the Short QTY field is blank or zero. |
Open Demand QTY |
Displays the quantity of this component needed for this operation sequence of this production order. The open demand quantity is calculated as follows: (current scheduled quantity) less (the quantity already issued). The (current scheduled quantity) is the number of components required for the operation sequence or batch production and includes the yield percentage. |
Available Supply QTY |
Displays the component quantity that this report estimates will be available in this business unit on the date and time of this row. This available supply quantity is calculated as follows:
The Available Supply QTY field does not include pegged supply or pegged demand. A pegged quantity is not considered available quantity because it is already committed to a specific demand or supply. |
Total Available/Reserved QTY |
The Total Available QTY field displays the total available quantity that is currently in this business unit. This field includes:
The Reserved Qty field displays the component quantity that is soft-reserved within this business unit. |
Total Demand/Incoming Supply QTY |
The Total Demand QTY field displays the sum of all open demand for this component in the date range specified. This field includes pegged quantities. Based on your selection criteria on the Material Readiness Report-Supply/Demand page, demand can include production orders (ready, unready, or both), sales orders, work orders, material stock requests, interunit transfers, planned transfers, and planned production. The date range is specified in the Past Due Demand Days and Future Demand Days fields. The current production order is included in this total. The Incoming Supply QTY field includes stock of this component that is going to be delivered to this business unit in the date range specified. The component's available quantity within a business unit will be increased when incoming supply is received into the business unit. This field includes pegged quantities. Based on your selection criteria on the Material Readiness Report-Supply/Demand page, the incoming supply can include stock from requisitions, purchase orders (order quantity less the quantity that has already been received), interunit transfers coming into the business unit, received quantities that are in the Putaway Staging tables, production orders (scheduled quantity less the already completed quantity), planned purchase orders, planned transfers, and planned production orders. The date range is specified in the Past Due Supply Days and Future Supply Days fields. |
This example illustrates the fields and controls on the Example of the Component Summary section of the Material Readiness report. You can find definitions for the fields and controls later on this page.
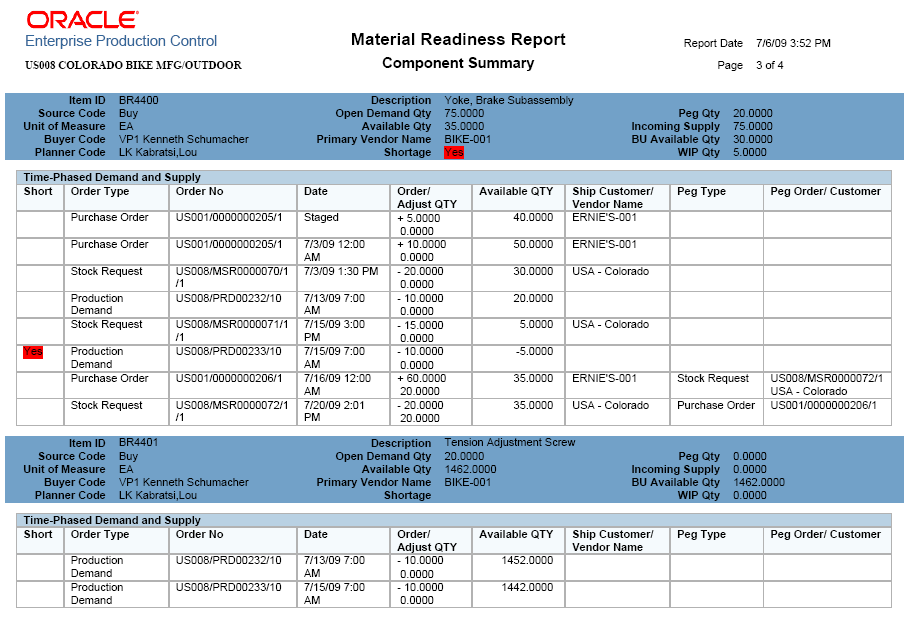
The component summary section of the Material Readiness report displays demand and supply by component item ID and determines if there is enough available quantity to meet the demand. The quantities displayed on this report are calculated based on your selection criteria on the run control for the Material Readiness Report (Production Control, Process Production, Release Production, Material Readiness Report).
For each component the following fields are displayed:
Field or Control |
Description |
---|---|
Unit of Measure (in component heading) |
Displays the standard unit of measure used for this component in all quantity fields. |
Open Demand Quantity (in component heading) |
Displays the sum of all open demand for this component in the date range specified. This field includes pegged quantities. Based on your selection criteria on the Material Readiness Report-Supply/Demand page, demand can include production orders (ready, unready, or both), sales orders, work orders, material stock requests, interunit transfers, planned transfers, and planned production. The date range is specified in the Past Due Demand Days and Future Demand Days fields. The details for the open demand quantity are displayed in the rows under the component heading. For example, in the page shot above the open demand quantity of 75 EA for item ID BR4400 is a total of the negative quantities in the Order/Adjust QTY column, including the stock requests and production IDs (20 + 10 + 15 + 10 + 20). |
Available Qty (in component heading) |
Displays the total component quantity that is currently available in this business unit. This field includes the BU Available Qty field (in the component heading of this page), plus the quantity in the WIP locations of this business unit if you have selected the Incl WIP in Starting Qty check box on the Material Readiness Report-Supply/Demand page. |
Shortage (in component heading) |
Displays Yes when there is not enough supply to meet the demands for this component. |
Peg Qty (in component heading) |
Displays the amount of incoming supply that is pegged to a demand. This field displays zero if you have not selected the Report Peg Information check box on the Material Readiness Report run control page. Due to the additional amount of data, selecting the Report Peg Information check box may slow the performance of this report. |
Field or Control |
Description |
---|---|
Incoming Supply (in component heading) |
Displays the quantity of component stock that is going to be delivered to this business unit in the date range specified. The component's available quantity within a business unit will be increased when incoming supply is received into the business unit. This field includes pegged quantities. Based on your selection criteria on the Material Readiness Report-Supply/Demand page, the incoming supply can include stock from requisitions, purchase orders (order quantity less the quantity that has already been received), interunit transfers coming into the business unit, received quantities that are in the Putaway Staging tables, production orders (scheduled quantity less the already completed quantity), planned purchase orders, planned transfers, and planned production orders. The date range is specified in the Past Due Supply Days and Future Supply Days fields. The details for the incoming supply quantity are displayed in the rows under the component heading. For example, in the page shot above the incoming supply quantity of 75 EA for item ID BR4400 is a total of the positive quantities in the Order/Adjust QTY column. In this example, incoming supply consists of three purchase orders (5 + 10 + 60). |
BU Available Qty (in component heading) |
Displays the total component quantity that is currently available in this business unit. Available quantity is calculated as follows:
The quantities in WIP locations are reserved; therefore, not included in this quantity. |
WIP Qty (in component heading) |
Displays the component quantity within the WIP locations of this business unit. |
Time-Phased Demand and Supply (group box) |
Provides the details to the Open Demand Qty field and the Incoming Supply field in the component header and highlights any time period where a shortage will occur. This grid displays the changes to the available quantity of the component within the date range specified on the Material Readiness Report-Supply/Demand page. Rows display an increase in available quantity due to incoming supply and a decrease due to demand. |
Short |
Displays Yes on the date/time row where a shortage of component quantity will occur. |
Order Type |
Displays the type of demand or supply on the current row. The types of demand can include production orders, sales orders, work orders, material stock requests, interunit transfers, planned transfers, and planned production. The types of incoming supply can include requisitions, purchase orders, interunit transfers coming into the business unit, received quantities that are in the Putaway Staging tables, production orders, planned purchase orders, planned transfers, and planned production orders. |
Order No |
Displays the source or destination business unit, order number, and line number of the demand or supply. For demand-type production IDs, the business unit, production ID, and operation sequence are displayed. For demand-type production schedules, the business unit, production area, and operation sequence are displayed. |
Date |
Displays the date and time when the component quantity is needed for this demand or when the incoming supply is scheduled to be received in the business unit. The word Staged is displayed if the incoming supply is currently in the Putaway Staging tables. For example, in the previous page shot, row 1 shows a purchase order that has been received but not yet putaway. In addition, rows 2 and 3 show past due supply and demand because the report date is 7/6, the purchase order was due 7/3, and the stock request was due to ship on 7/3. Also, notice that rows 5 and 6 both show demand that is needed on 7/15 but based on priorities, the stock request gets the quantity before the production ID even though the production ID has an earlier date/time. |
Order/Adjust QTY |
The Order QTY field displays the open quantity on the order. Incoming supply is shown as a positive quantity and demand is shown as a negative quantity. The Adjust QTY field displays the reserved quantity and the amount of the open quantity that is pegged for this demand or supply row. For supply transactions, the Adjust Qty field is only peg quantity, but for demand transactions, the Adjust QTY field is the sum of pegged quantity and reserved quantity. This field is populated if you have selected the Report Peg Information check box on the Material Readiness Report run control page. Due to the additional amount of data, selecting the Report Peg Information check box may slow the performance of this report. |
Available QTY (in the Time-Phased Demand and Supply group box) |
Displays the estimated available quantity for this date/time row. The first row is calculated by starting with the Available Qty field in the component heading and then adding or subtracting the Order QTY field in the current row. Incoming supply increases the available quantity while demand decreases the available quantity. Following rows are calculated by taking the amount in the Available QTY field of the previous row, then adding or subtracting the Order QTY field in the current row. For example, in the previous page shot, row 7 displays a purchase order that is pegged to a stock request. The purchase order quantity is for 60 each; 20 of that 60 is pegged to a stock request. The Adjust Qty field represents the 20 that is pegged. The impact to available quantity is a positive 40 (that is, 60 less 20). The Peg Order/Customer column displays the stock request that is pegged to the purchase order. Also, the purchase order quantity does not change the Available QTY field because its pegged. In addition, in the previous page shot, row 8 displays a stock request that is pegged to a purchase order. The Adjust Qty represents the pegged quantity. Again, the stock request quantity does not change the Available QTY field because its pegged. |
Ship Customer/Supplier Name |
The customer name is displayed for sales orders, material stock requests, and demand-side production IDs with a configured item or pegged quantity. The supplier name is displayed for requisitions or purchase orders. For interunit stock requests, the source or destination business unit is displayed. |
Peg Type |
Displays the type of demand or supply that this row is linked to in a peg chain. For example, if the current row is a purchase order (supply-side), then it can be linked to a material stock request (demand-side). This column is populated if you have selected the Report Peg Information check box on the Material Readiness Report run control page. Due to the additional amount of data, selecting the Report Peg Information check box may slow the performance of this report. |
Peg Order/Customer |
Displays the business unit, order number, line number, and customer name of the order that this row is linked to in a peg chain. For example, if the current row is a purchase order (supply-side), and it is linked to a material stock request (demand-side); then this row displays the information about the material stock request. The word Multiple is displayed if the current row is pegged to more than one transaction. This column is populated if you have selected the Report Peg Information check box on the Material Readiness Report run control page. Due to the additional amount of data, selecting the Report Peg Information check box may slow the performance of this report. |
Formatting the Material Readiness Report with Oracle's BI Publisher
The Material Readiness Report uses the BI Publisher to create the layout of the report. BI Publisher is a template-based reporting solution that separates the data extraction process from the report layout and enables the reuse of extracted application data into multiple report layouts. You can change the format or layout of this report without changing the underlying program that controls the business logic. The format and layout includes the appearance of the report and addition or removal of fields on the report as long as those fields are available as part of the SF_MATRDY application engine process.
The delivered data for the Material Readiness Report in BI Publisher (Reporting Tools, BI Publisher) includes:
Report Definition: SF_MATRDY
Data Source ID: SF_MATRDY_DATA
Template ID: SF_MATRDY_1
Template File: SF_MATRDY_ENG.RTF
Page Name |
Definition Name |
Usage |
---|---|---|
Material Readiness Report Page |
RUN_SF_MTLRDY |
Enter search criteria and options to run the material readiness report. This report determines the material readiness of a production run by checking the available quantity of component materials. |
RUN_SF_MTLRDY_SD |
Select the sources of supply and demand used when calculating the material readiness report. |
Use the Material Readiness Report page (RUN_SF_MTLRDY) to enter search criteria and options to run the material readiness report.
This report determines the material readiness of a production run by checking the available quantity of component materials.
Navigation:
This example illustrates the fields and controls on the Material Readiness Report run control page (1 of 2). You can find definitions for the fields and controls later on this page.
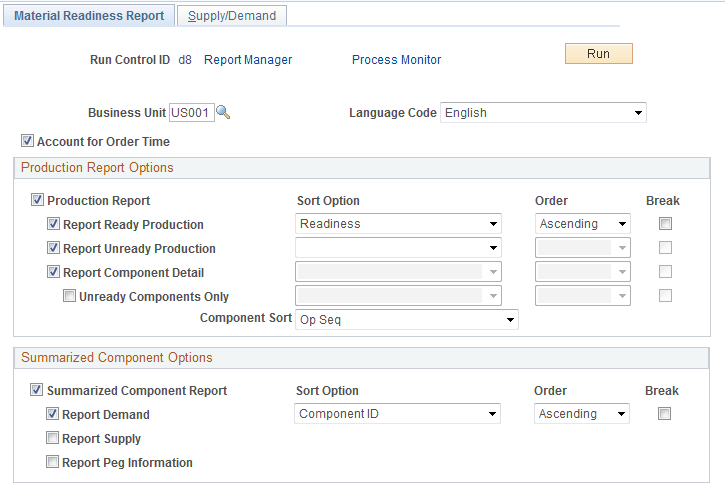
This example illustrates the fields and controls on the Material Readiness Report run control page (2 of 2). You can find definitions for the fields and controls later on this page.
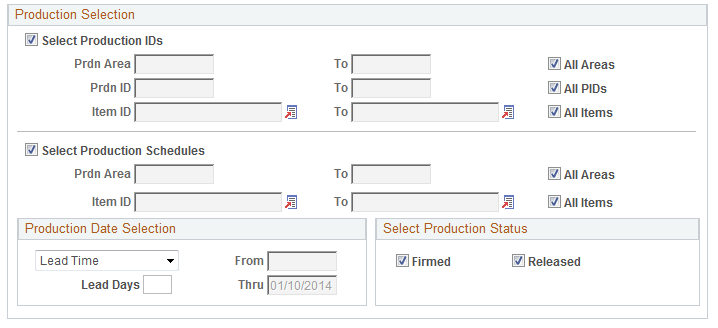
The Material Readiness Report run control page includes the selection criteria and options to produce the material readiness report. The material readiness report can include one or both of the following report options:
Production Detail section
Component Summary section
Field or Control |
Description |
---|---|
Unit |
Enter the PeopleSoft Manufacturing business unit of the production run. |
Account for Order Time |
Select this check box to sort supply and demand by date and time. Deselect this check box to ignore due time when determining readiness. The system assumes that the supply for a date is available for the demand needed that day. |
Production Report Options group box
Use this group box to generate the production detail section of the material readiness report and to enter the options for this section. The production detail section displays production readiness by production ID or production schedule.
Field or Control |
Description |
---|---|
Production Report |
Select this check box to include the production detail section within the material readiness report. |
Report Ready Production and Report Unready Production |
Select the Report Ready Production check box to display production IDs and production schedules that are ready for production in the report. Select the Report Unready Production check box to display production IDs and production schedules that are not ready for production in the report. Use these check boxes to determine what is displayed on the report output. These options give you the flexibility to tailor the report to search specifically for production that is ready to go or to look for production that is not ready. Select one or both check boxes. By deselecting one of these check boxes you are limiting the report output to just ready production or just unready production. |
Sort Option |
Specify up to four sort levels for the production report section of the material readiness report. Within each level, you can sort by:
Each lower sort is within the sort specified above it. For example, you might want to sort the production by readiness, then sort by the production ID, and then sort the start date. |
Order |
Select Ascending or Descending for the corresponding Sort Option field. |
Break |
Select this check box to create a page break for every value change in the corresponding sort option. For example, if you have selected the sort option of Production and the production ID changes, then a new page is started. |
Report Component Detail |
Select this check box to display the components associated with production and each component's readiness status. If a specific production ID or production schedule does not have component requirements, (for example, a rework or teardown might not have components) then the production is flagged as Ready. |
Unready Components Only |
Select this check box to display only the unready components on the report component detail section of the production report. This option enables you to focus on the issues preventing the start of production. This check box is only available if you have selected the Report Component Detail check box above. |
Component Sort |
Select the sort order for the report component detail section of the production report. The sort options are:
This check box is only available if you have selected the Report Component Detail check box above. |
Summarized Component Options group box
Use this group box to generate the component summary section of the material readiness report and to enter the options for this section. The component summary section displays time-phased demand and supply quantities by component item ID. This enables you to view the impact that each demand or supply order has on the available quantity and determine if there is enough available quantity to meet your demand.
Field or Control |
Description |
---|---|
Summarized Component Report |
Select this check box to include the component summary section within the material readiness report. |
Report Demand |
Select this check box to display the details of demand for this component. Demand can include production orders, sales orders, work orders, material stock requests, planned transfers, and planned production that need this component. |
Report Supply |
Select this check box to display the details of supply for this component. Supply can include available stock in the business unit plus incoming supply from purchase orders, completed production, or material stock requests. |
Report Peg Information |
Select this check box to display additional information about a peg quantity. Additional information includes the customer or supplier associated with a pegged quantity. Note: Due to the additional amount of data, selecting the Report Peg Information check box may slow the performance of this report. |
Sort Option |
Select how the component summary section should be sorted on the report. The options are:
|
Order |
Select Ascending or Descending for the Sort Option field. |
Break |
Select to create a page break at the sort level chosen in the Sort Option field. |
Production Selection group box
Use this group box to enter the search criteria to select the production IDs and production schedules to be evaluated by the material readiness report for component availability.
Field or Control |
Description |
---|---|
Select Production IDs |
Select this check box to include production IDs in this report. |
Select Production Schedules |
Select this check box to include production schedules in this report. |
Prdn Area and To |
Define one production area or a range of production areas to select specific production IDs or production schedules. The page location of these fields determine whether they impact the production ID selection or the production schedule selection. |
Prdn ID and To |
Enter a specific production ID or a range of production ID to be included on the material readiness report. |
Item ID and To |
Define one item ID or a range of items to select specific production IDs or production schedules. The page location of these fields determine whether they impact the production ID selection or the production schedule selection. |
All Areas |
Select this check box to include all production areas within this business unit in your search criteria. When this check box is selected, the Prdn Area field is deselected. The page location of this check box determines whether it impacts the production ID selection or the production schedule selection. |
All PIDs |
Select this check box to include all production IDs within this business unit in your search criteria. When this check box is selected, the Prdn ID field is deselected. The selected production IDs must also meet the additional selection criteria on this page. |
All Items |
Select this check box to include all item IDs within this business unit in your search criteria. When this check box is selected, the Item ID field is deselected. The page location of this check box determines whether it impacts the production ID selection or the production schedule selection. |
Production Date Selection |
Enter date selection criteria for production IDs or production schedules that are due to start within the days selected. The options are:
|
Select Production Status |
Select the status of the production IDs and production schedules to be included in the material readiness report. Select the Firmed check box, the Released check box or both. |
Use the Material Readiness Report- Supply/Demand page (RUN_SF_MTLRDY_SD) to select the sources of supply and demand used when calculating the material readiness report.
Navigation:
This example illustrates the fields and controls on the Material Readiness Report-Supply/Demand page (1 of 2). You can find definitions for the fields and controls later on this page.
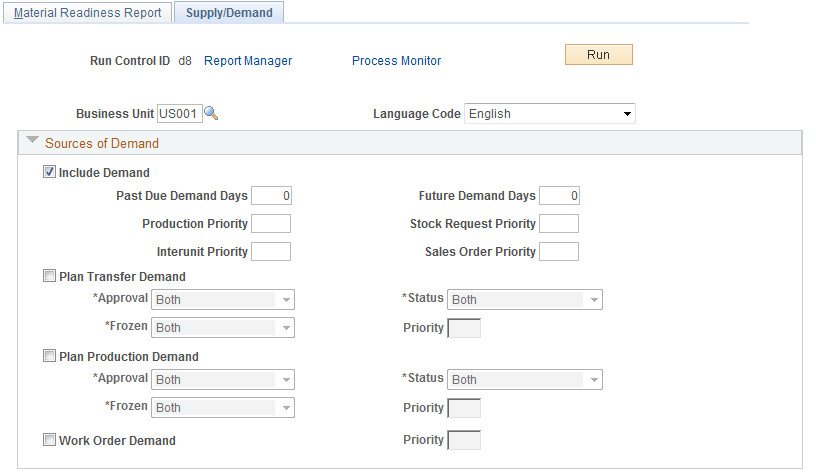
This example illustrates the fields and controls on the Material Readiness Report-Supply/Demand page (2 of 2). You can find definitions for the fields and controls later on this page.
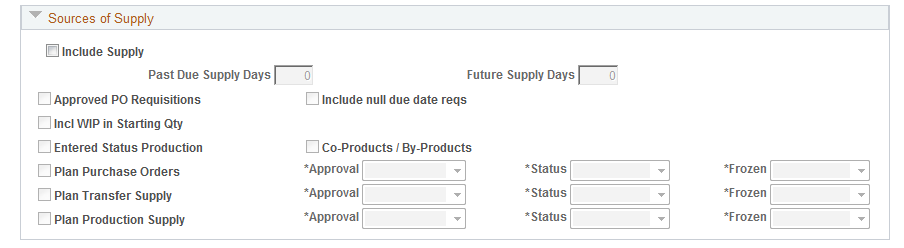
The Material Readiness Report- Supply/Demand run control page provides the selection criteria for the type of demand and supply to be included in the calculation of the material readiness report.
Sources of Demand group box
Use this group box to determine what sources of demand are used in the calculation of the material readiness report. The component's available quantity within the business unit is reduced by demand for this same component from other production orders, sales orders, work orders, material stock requests, interunit transfers, planned transfers, and planned production.
Field or Control |
Description |
---|---|
Include Demand |
Select this check box to include other demands for the component quantity in the material readiness calculation, such as other production orders, sales orders, work orders, material stock requests, interunit transfers, planned transfers, and planned production. When this check box is not selected, the material readiness calculation determines if there is enough stock to meet production requirements by comparing the component quantity needed to the current quantity available in the business unit. |
Past Due Demand Days |
Use this field to help determine the time range to collect unfulfilled demand. Enter the number of days before today's date to include past due demand. For example, if you enter 5 days and today is June 5th, then the readiness calculation includes any unfulfilled demand that was needed on June 1st through today. |
Future Demand Days |
Use this field to help determine the time range to collect unfulfilled demand. Enter the number of days into the future to include future demand. For example, if you enter 10 days and today is June 5th, then the readiness calculation includes any unfulfilled demand that will be needed from today through June 15th. |
Priority Fields |
Use the priority fields to determine the relative priority for various types of demand. If two or more transactions have the same due date, then the entries here determine how the current component stock quantity is distributed. Use the following fields to prioritize demand types:
For example, if you enter 1 in the Sales Order Priority field, 2 in the Stock Request Priority field, 3 in the Production Priority field, and 4 in the Interunit Priority field, then the material readiness report distributes available quantity needed on the same date/time to a sales order first, a material stock requests second, a production order third, and a interunit transfer fourth. These priority settings only impact the material readiness report. |
Plan Transfer Demand |
If PeopleSoft Supply Planning is installed, select this check box to include planned transfers in the demand side of the material readiness calculation. Define which planned transfers should be included based on the Approval, Status (planned, firm planned, or both), and Frozen fields in this row. Use the Priority field to determine the relative priority of planned transfers compared to other types of demand. |
Plan Production Demand |
If PeopleSoft Supply Planning is installed, select this check box to include planned production in the demand side of the material readiness calculation. Define which planned production should be included based on the Approval, Status (planned, firm planned, or both), and Frozen fields in this row. Use the Priority field to determine the relative priority of planned production compared to other types of demand. |
Work Order Demand |
If PeopleSoft Maintenance Management is installed, select this check box to include work orders in the demand side of the material readiness calculation. Use the Priority field to determine the relative priority of work orders compared with the other sources of demand (production orders, sales orders, material stock requests, interunit transfers, planned transfers, and planned production). |
Sources of Supply group box
Use this group box to determine what sources of supply are used in the calculation of the material readiness report. The component's available quantity within a business unit is increased by incoming supply from purchase orders, interunit transfers, or production.
Field or Control |
Description |
---|---|
Include Supply |
Select this check box to include other sources of supply for the component quantity in the material readiness calculation, such as purchase orders, incoming interunit transfers, or other production. When this check box is not selected (default), the material readiness calculation uses the current quantity available in the business unit as the source of supply. |
Past Due Supply Days |
Use this field to help determine the time range to collect incoming supply. Enter the number of days before today's date to include past due supply from incoming supply sources, such as; purchase orders, incoming interunit transfers, or other production. For example, if you enter 5 days and today is June 5th, then the readiness calculation includes any incoming supply that was due on June 1st through today. |
Future Supply Days |
Use this field to help determine the time range to collect incoming supply. Enter the number of days into the future to include future supply from incoming supply sources, such as; purchase orders, incoming interunit transfers, or other production. For example, if you enter 10 days and today is June 5th, then the readiness calculation includes any incoming supply that will be received from today through June 15th. |
Approved PO Requisitions |
If PeopleSoft Purchasing is installed, select this check box to include approved requisitions in the supply side of the material readiness calculation. Only approved requisitions that specify the PeopleSoft Inventory business unit and a due date are counted. |
Include null due date reqs |
Select this check box to include approved requisitions with a blank due date. The report uses today's date as the due date for these requisitions. This check box is only available if you have selected the Approved PO Requisitions check box. |
Incl WIP in Starting Qty |
Select this check box to add the available quantity within a WIP location to the current available quantity of the business unit. A WIP location is a material storage location within the business unit that is defined as a WIP location. |
Entered Status Production |
Select this check box to include production orders in the Entered status in the supply side of the calculation. |
Co-Products / By-Products |
Select this check box to include co-products and by-products in the supply side of the calculation. |
Plan Purchase Orders |
If PeopleSoft Supply Planning is installed, select this check box to include planned purchase orders in the supply side of the calculation. Define which planned purchase orders should be included based on the Approval, Status (planned, firm planned, or both), and Frozen fields in this row. |
Plan Transfer Supply |
If PeopleSoft Supply Planning is installed, select this check box to include planned transfer orders in the supply side of the calculation. Define which planned transfers should be included based on the Approval, Status (planned, firm planned, or both), and Frozen fields in this row. |
Plan Production Supply |
If PeopleSoft Supply Planning is installed, select this check box to include planned production orders in the supply side of the calculation. Define which planned production should be included based on the Approval, Status (planned, firm planned, or both), and Frozen fields in this row. |