Setting Up, Viewing, and Recording Material Usage from the Service Order
To define failure codes types, use the Failure Code (RF_FAILURE_CD) component. To load data into the tables for this component, you can also use the RF_FAILURE_CD_SCI component interface.
This section provides an overview on material usage and discusses how to define failure codes, view required materials and track time, materials, and expenses associated with a service order.
Page Name |
Definition Name |
Usage |
---|---|---|
RF_FAILURE_CD |
Define failure codes to be used for removed materials. |
|
RF_MAT_REQUIRED |
Lists all items and their quantities needed for the service. You can also view item availability and balances. |
|
RF_SO_TIME_MAT_EXP |
Record time, material, and expense information. You cannot log time, material, and expense entries against a service order until the service order has been saved. |
See PeopleSoft Inventory
This section discusses:
Material usage.
Automatic receiving.
Material removed from customer sites.
Material Usage
Technicians record the quantity of material used to perform the work for a service order activity on the Time Material Expense page for the service order. When an item ID and quantity is entered and saved, the PeopleSoft CRM system determines whether a corresponding installed product exists for the item.
Depending on the rules governing creation and updates for installed products, an installed product may exist if an order for the material was placed using PeopleSoft Order Capture, Order Capture Self Service or if an automatic shipping notification (ASN) message for the item was sent to the PeopleSoft CRM system.
If an installed product exists, the system updates the status of the record by using the rules that are established on the Installed Product page in the Product Definition component.
The system publishes the Inventory Adjustment EIP to stage negative adjustment transactions in your inventory system. Your inventory system processes the staged adjustment transactions to decrease the quantity in the storage location that is associated with the selected technician's good truck stock by the usage quantity.
If your system integrates with PeopleSoft Inventory, the system decreases the quantity in the technician's good truck stock storage location when the Inventory Adjustment process is run for the staged transaction. If required, the system also creates a new installed product for the item by using rules that are defined for the corresponding product on the Installed Product page in the Product Definition component.
Note: When you are recording material usage, you may choose a technician from those assigned to any service order activity. The system records the user ID of the person who entered the usage transaction. If the system cannot determine the user ID of the technician who entered the transaction, it uses the ID of the lead technician. On the PeopleSoft SCM side, the inventory adjustment (decrease) is made against the good storage location of the technician who used the materials.
This diagram illustrates the material usage transaction process.
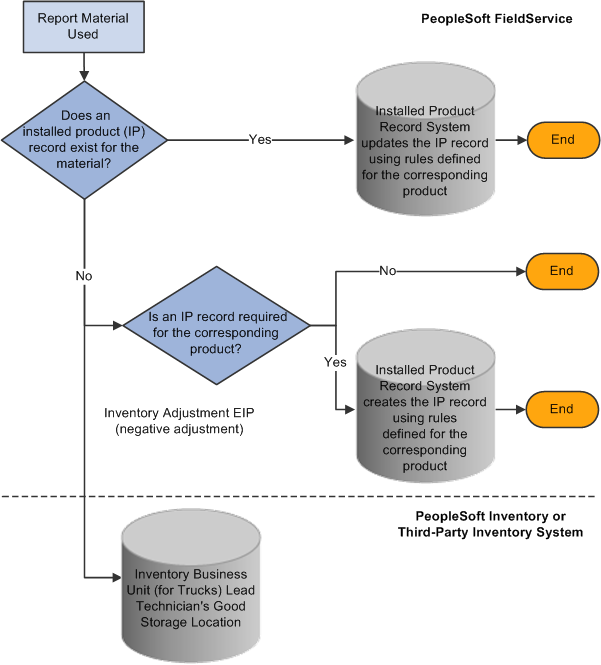
Note: Because the order of positive and negative adjustment transactions to inventory storage locations cannot be predicted, set up your inventory system to allow transactions to drive inventory quantity balances to be negative.
Automatic Receiving
In field service business units that enable automatic receiving, technicians use the Time Material Expense page for the service order to record the portion of the material shipment that was not required to complete the work on the service order activity. The system automatically runs the expected receipts to prepopulate the Material grid on the page.
The system adds the used and unused quantity to derive the receipt quantity and increases the selected technician's good storage location in PeopleSoft Inventory or your third-party inventory system.
If automatic receiving is enabled, technicians enter usage information for a material shipment in the Material grid on the Time Material Expense page of the Service Order.
When you save the Service Order, the PeopleSoft CRM system stages the appropriate receipt transactions in your purchasing or inventory systems by using the PO Receipt EIP for purchase orders and the Interunit Receipt EIP for interunit transfers. The system derives the receipt quantity by adding the used and not used quantities.
Material Removed from Customer Sites
Technicians record material that they remove from a customer's site by selecting Removed from the Action field on the Usage Details tab on the Time Material Expense page for the service order.
Note: When you record material removed from a customer site, you may choose the technician from those assigned to the service order activity. The system records the user ID of the person who entered the removal transaction. If the system cannot determine the user ID of the technician who entered the transaction, it uses the ID of the lead technician. On the PeopleSoft SCM side, the inventory adjustment (increase) is made against the defective storage location of the technician who removed the materials.
When an item quantity is entered in the Usage Details grid and the page is saved, the PeopleSoft CRM system publishes the Inventory Adjustment EIP to stage positive adjustment transactions in your inventory system. Your inventory system processes the staged adjustment transactions to increase the quantity in the storage location that is associated with the lead technician's defective truck stock by the removal quantity.
If your system integrates with PeopleSoft Inventory, the system increases the quantity in the selected technician's defective truck stock storage location when the Inventory Adjustment process is run for the staged transaction.
If the item that is associated with the product on the service order header and the serial number on the service order header are the same as the item and serial number on the Usage Details grid, saving the item quantity also triggers PeopleSoft CRM to check the installed products for the customer on the service order activity.
The system sets the installed product for the removed item to Uninstalled. Before saving, if an item that is associated with an installable product is also listed on the Usage Details grid, the system inserts a new installed product for the replacement item and serial number with a status of Installed.
Note: To set up statuses, use the Installed Product page of the Product component.
While you can use the same default values across all products by applying the default values at the product level with a click of a button, you can also overwrite the default values for specific products.
If the system replaces the installed product, it also determines whether any of the customer's agreement lines reference the removed item as a product under service. If the removed item is referenced as a product under service, the system removes the obsolete line from the record for the product under service and inserts a new line representing the replacement item. If preventive maintenance is available to the installed product of the removed item, it is transferred and made available to the replacement installed product.
If the removed item is defined as a consumable item on the Item Definition page, no adjustment transaction is triggered. It is expected that the consumable item is thrown away rather than returned to the truck. However, you should record removal of consumable items using the Usage Details tab on the Time Material Expense page so that the system can make appropriate changes to the customer's installed product and the products under service on the associated agreement line.
This diagram illustrates how the integration between the PeopleSoft CRM system and your inventory and purchasing system supports recording the removal of material from a customer site.
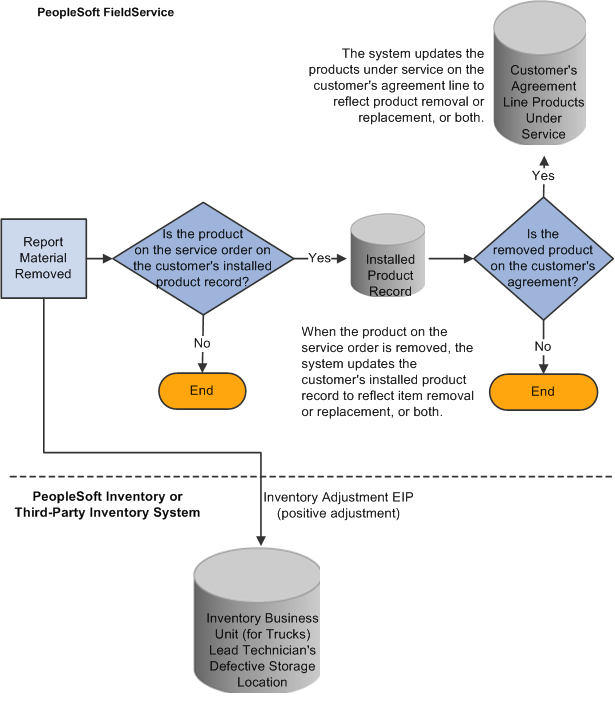
Your business processes dictate how removed material in a technician's defective storage location should be handled. Typically, this stock is transferred to a distribution center's inspection storage location by using the inventory system. At the distribution center's inspection location, a decision is made to scrap, recycle, repair, or restock the item in available inventory stores.
See PeopleSoft Inventory
Use the Failure Codes page (RF_FAILURE_CD) to define failure codes to be used for removed materials.
Navigation:
This is the first of two examples illustrating the fields and controls on the Failure Codes page.
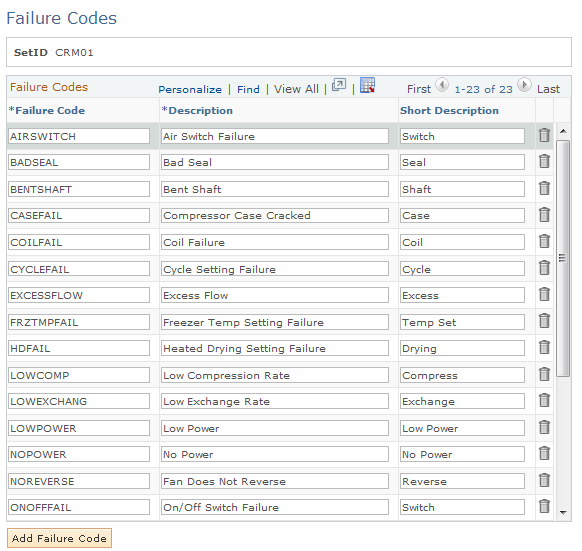
Field or Control |
Description |
---|---|
Failure Code |
Enter a failure code that can be used when specifying removed items on the Time Material Expense page. Failure codes identify what went wrong with parts that caused them to be removed from customers' sites. You can enter up to 10 alphanumeric characters. |
Add Failure Code |
Click to add a new failure code. |
Use the Service Order - Required Material page (RF_MAT_REQUIRED) to lists all items and their quantities needed for the service.
You can also view item availability and balances.
Navigation:
This example illustrates the fields and controls on the Service Order - Required Material page.
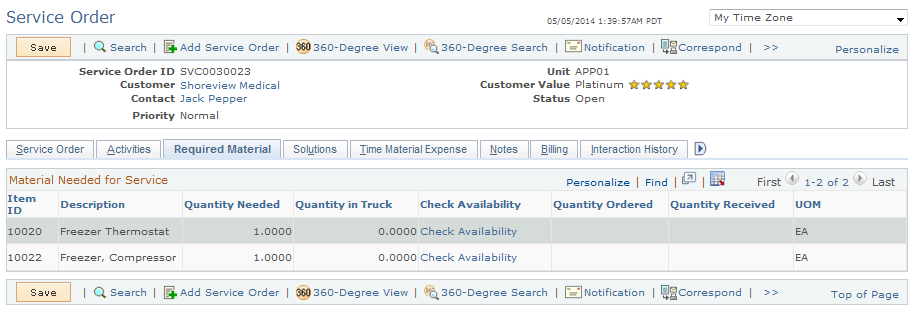
Use this page to view the required materials for the service order.
Use the Service Order - Time Material Expense page (RF_SO_TIME_MAT_EXP) to record time, material, and expense information.
Navigation:
This is the first of two examples illustrating the fields and controls on the Service Order - Time Material Expense page.
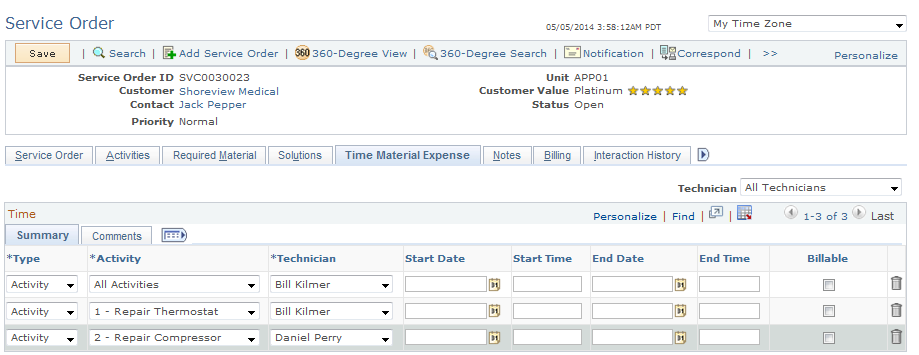
This is the second of two examples illustrating the fields and controls on the Service Order - Time Material Expense page.
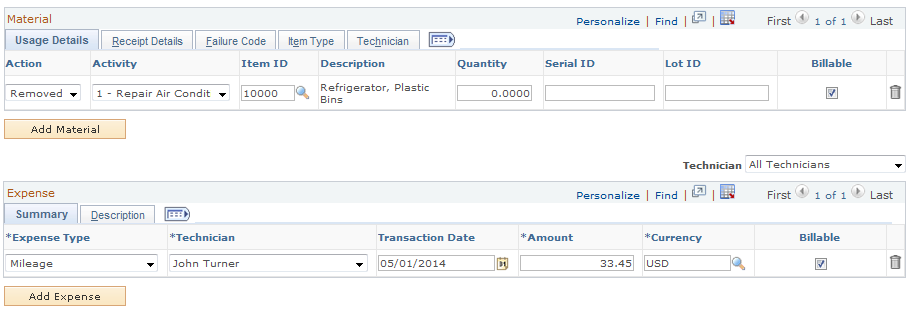
Use this page to record time, material, and expense information.